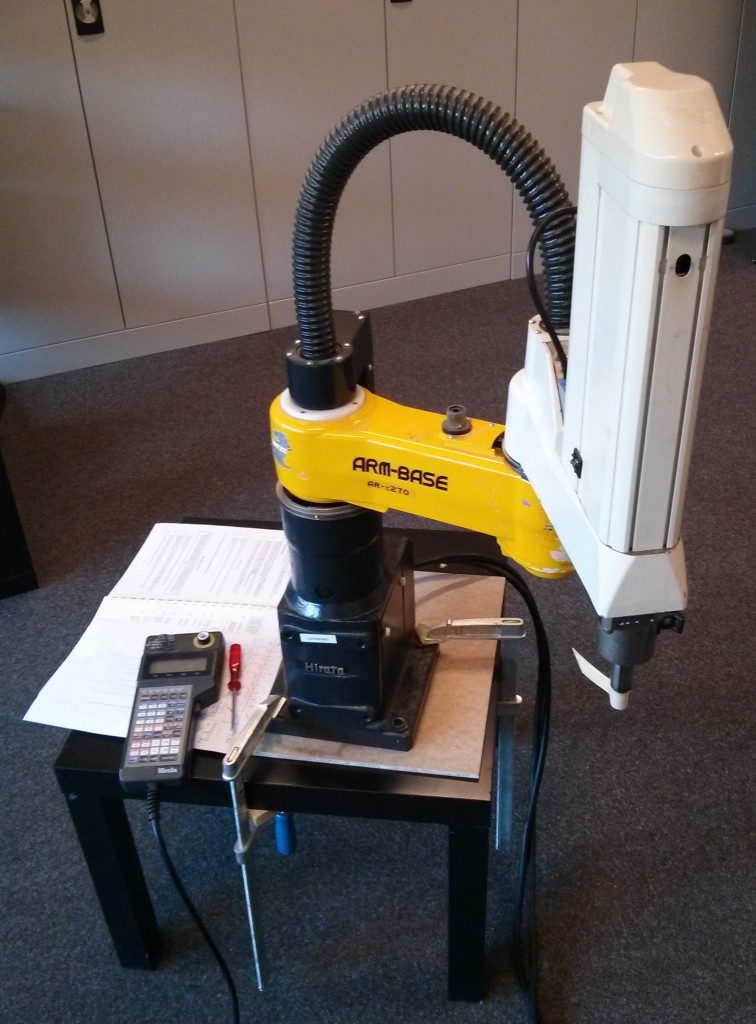
Recently I bought a Scara-Robot from Ebay. Its an older model with an outdated control. Motors, servos and encoders are in working condition. Using the Teach-Pendant I can move the Robot around.
My plan is to retrofit the control using linuxcnc. All IO will be done with a MESA 7i77+5i25 combo. I will try to reuse everything besides the original control.
There was quite a lot of documentation included in the Ebay auction, but most of it only covers software. No hints on the pinouts of the servo amp. The company producing the robot still exists, so I gave them a phone-call to request additional docs. I bought the manuals they offered me, but unfortunately they didn’t help at all. So I had to take the thing apart and try to reverse engineer the important parts. My findings so far are all in this 20150422_doku_hac214a.
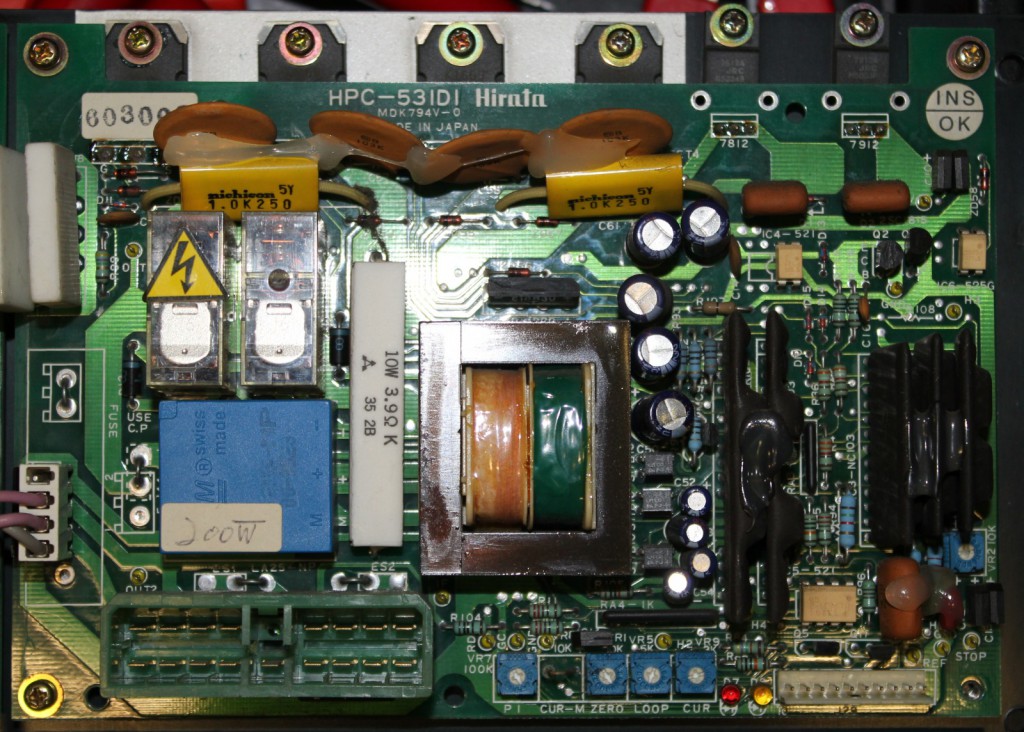
There are some diagramms for the motor- and encoder connections. And yes, the encoders produce a nice A/B-Signal:
As a next step I will test on of the amps standalone. Hopefully the info extracted so far is okay. Running the amps in velocity mode will make it easy to connect everything to the 7I77.